Electromagnetic Stirrer
Stirring metal with electromagnetic power
Reverberatory furnaces currently command the principal role in melting aluminum. This is due to the fact that equipment cost is low, operation is simple, and also as it is economical operate since the cost of fuel is comparatively low.
On the other hand, however, it has the disadvantage of difficulty in maintaining uniformity of components since, unlike the induction furnace, the reverberatory furnace does not have stirring action and temperature differences are generated between the bottom and surface of the molten metal and between the combustion chamber and the open well.
Although a mechanical or decompression type stirrer was used in the past to resolve this problem, development of a superior stirrer was in demand since operation and maintenance were troublesome.
Our electromagnetic stirrer is capable of mixing au of the molten metal in the furnace uniformly within an extremely short Period of time by means of a simple device utilizing the principle of a linear motor.
It is a revolutionary stirrer that nearly resolves the drawbacks of the reverberatory furnace and also conveniently resolves the problems of past stirring equipment.
Since SINFONIA TECHNOLOGY CO., LTD. has already manufactured various types of electromagnetic stirring equipment, full utilization of our -know-how will promise you highly effective results in the operation of reverberatory furnaces.
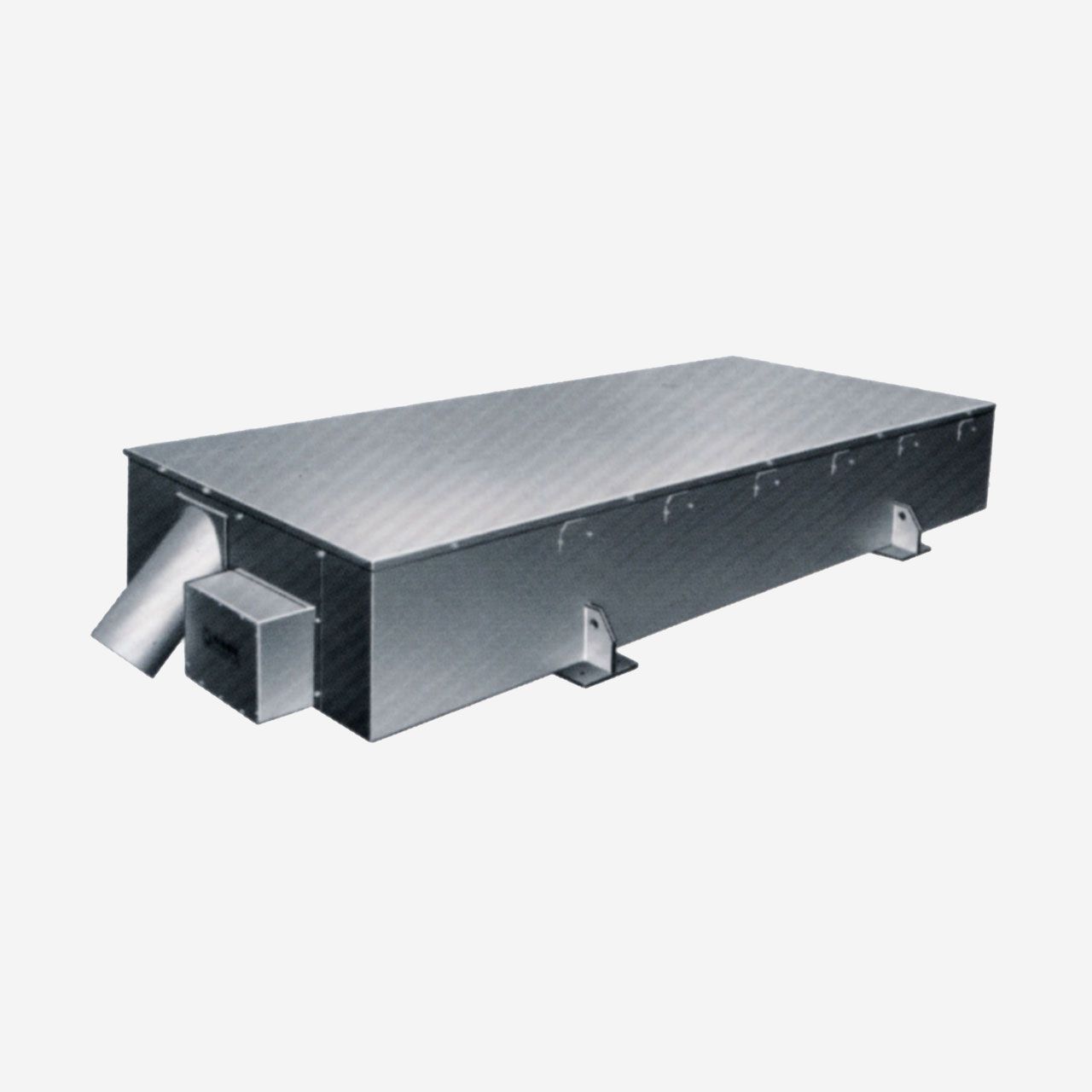
Furnace bottom type electromagnetic stirrer
This unit is nearly maintenance-free since it generates thrust by electromagnetic induction in the molten metal itself and does not touch the molten metal whatsoever.
Features
- Unifomalizes components and solves segregation!
Stirring action is extremely strong compared to other methods so molten metal in all parts of the furnace is rapidly and evenly stirred. The molten metal components are therefore uniform with no segregation whatsoever occurring. This unit is particularly effective for molten metal with high alloy content such as magnesium, titanium and silicon. - Substantial energy saving with high heat absorption!
s the surface of the molten in reverberatory furnaces is 100-150°higher in temperature than the bottom as it is sub1'eCted to radiation heat, thermal absorption tends to become poor. However, as the molten metal and cold charge are forced to touch when electromagnetic stirring is carried out, the temperature of the surface drops within a few minutes as the temperature of the top and bottom layer becomes uniform. Heat absorption therefore increases and high energy saving effects are realized as heat loss decreases. (fig1) -
Shortens melting time!
Heat conductivity of the cold material rises and the cold material melts more rapidly as the molten metal is caused to flow by stirring. The temperature of the overall molten metal drops at the same time with increased absorption of radiation heat. In addition to energy saving, the melting time is also therefore shortened. -
Prevents oxidation and improves yield!
Prevention of oxidation in the molten metal is important to improve yield. Electromagnetic stirring reduces oxidation as it lowers the surface temperature and, furthermore, it shortens the melting time. Yield is also increased by the folding-in effect of the cold charge into the molten metal. -
No manpower required and maintenance is simple!
Although manpower or a special vehicle is required during the stirring operation in conventional stirring equipment, this type of operation is entirely unnecessary with electromagnetic stirring as operation is fully automatic. Also, as there are no parts in direct contact with the molten metal, practically no maintenance is required. -
Accurate temperature control is possible!
It cannot be said that accurate temperature measurement of the molten metal has been made even with temperature checks if the temperature of the molten metal is nonuniform. However, accurate temperature control will be possible with the use of the electromagnetic stirrer as the overall temperature of the molten metal will be uniform. (fig2) -
Installation area of the reverberatory furnace reduced!
Since heat absorption of the surface of the molten metal improves, it will be possible to design furnaces with a deeper molten metal chamber and a smaller surface area. This will then enable reducing the size of the installation area.
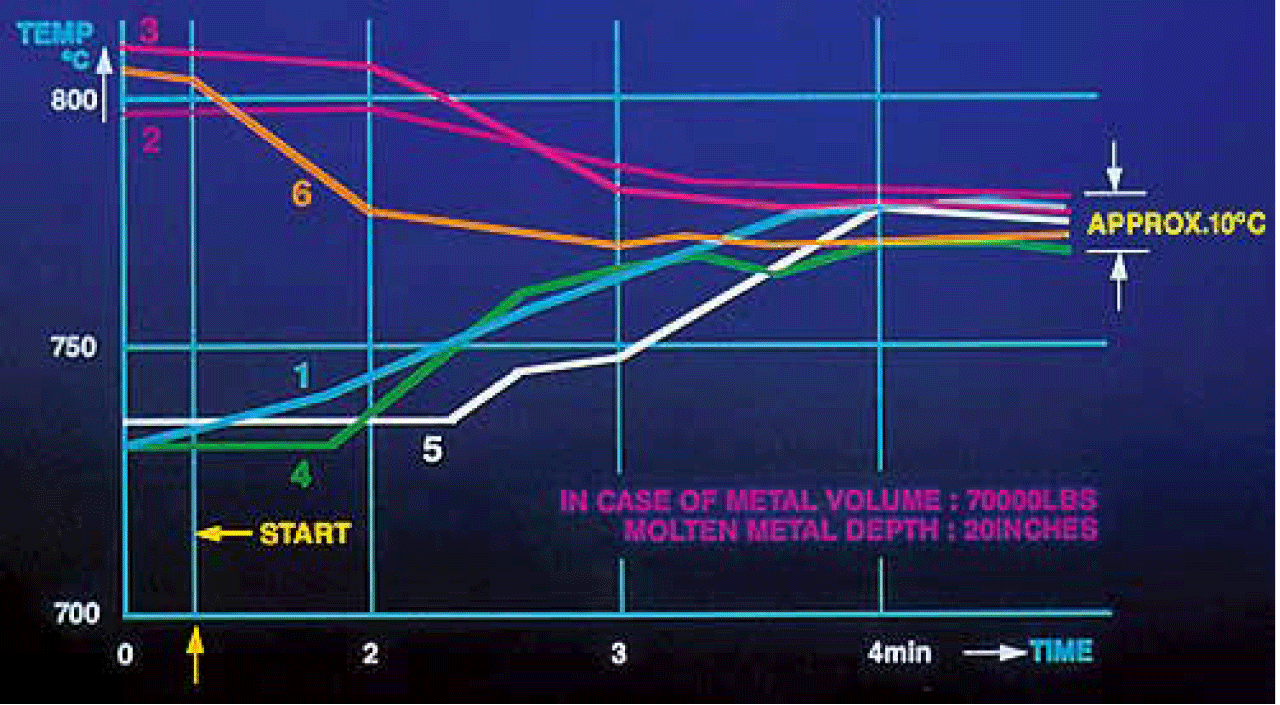
fig1. Temperature Uniformity
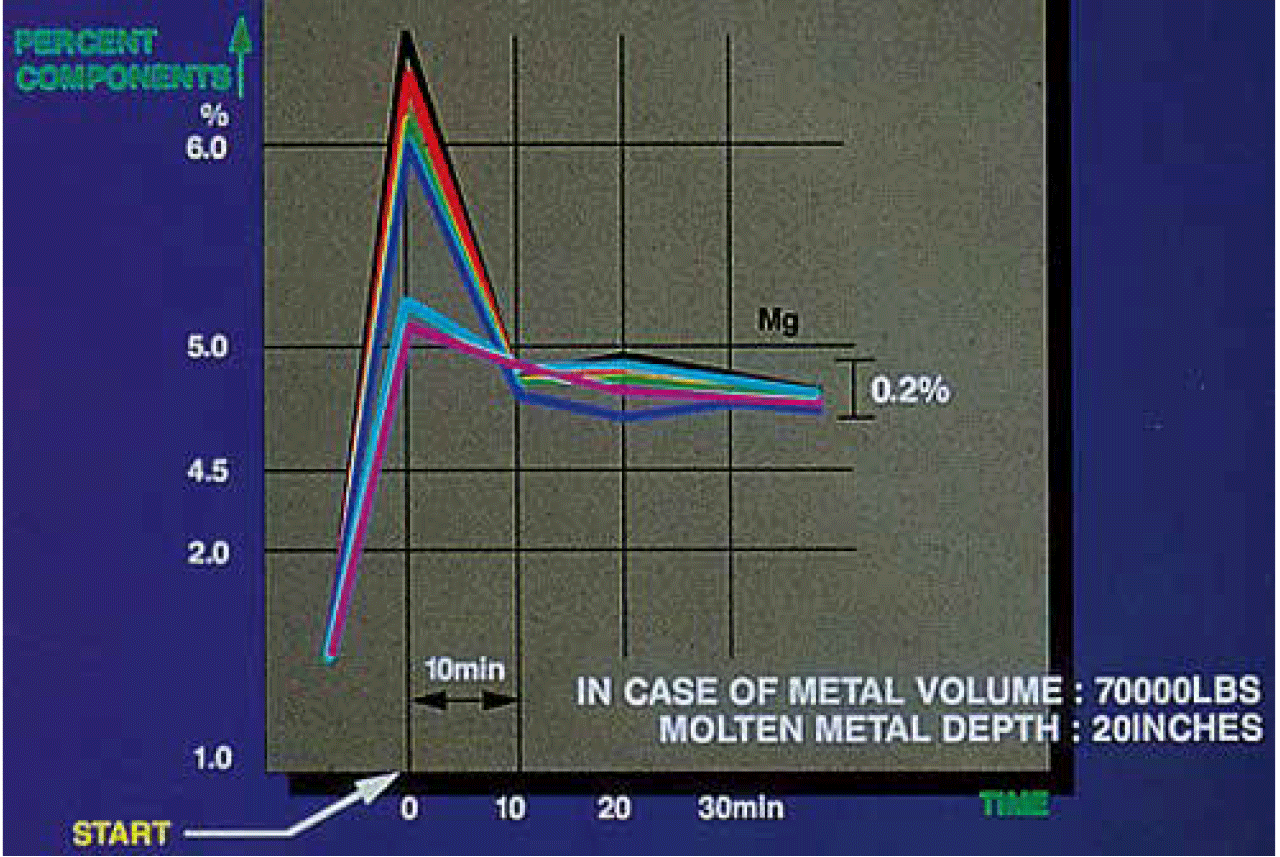
fig2. Components Uniformity
The Principle of Stirring
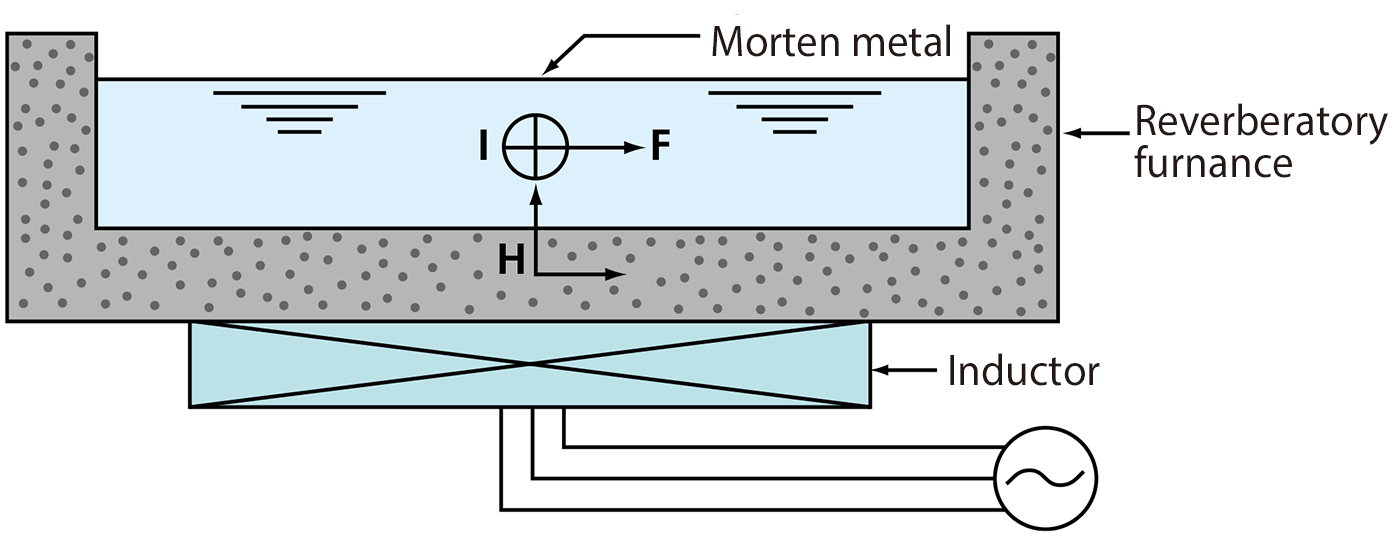
The electromagnetic stirrer utilizes the principle of a linear motor and differs from the conventional mechanical and decompression types as it is a noncontact stirrer in which no part touches the molten metal. As shown in the diagram, a coil installed at the bottom of the furnace generates a moving magnetic field (H) if a 3 phase AC voltage is applied to this coil (inductor). Electric power force is generated in the molten metal due to the action of the magnetic field (magnetic flux) and causes induction current (I) to flow (Fleming's right hand rule). This current then acts with the magnetic field of the inductor to induce electromagnetic force (F) in the molten metal according to Fleming's left hand rule. As this thrust moves in the direction of the moving magnetic field, the molten metal also moves. In other words, an stirring action is applied. Furthermore, as this thrust has components in the horizontal direction and in the vertical direction, the molten metal flows diagonally upwards and results in a uniform temperature in both the top and bottom layers of the molten metal.
Specification
Model | EMSA-M2 | EMSA-M1 | EMSA-ML | EMSA-L1 | |
---|---|---|---|---|---|
Use | Melting furnace Holding furnace |
||||
Furnace capacity (Ton) |
10~20 | 10~30 | 20~40 | 30~60 | |
Thickness of furnace bottom (mm) |
400 | 500 | 550 | 650 | |
Power consumption (KW) (Including EMSA&Blower) |
30 | 40 | 60 | 80 | |
Operation frequency (HZ) |
1.5 | 1 | 0.8 | ||
Rating current (A) |
250 | 260 | 280 | 400 | |
Size of the stirrer unit (mm) |
1,220Wx2,430Lx 440H | 1,270Wx2,870Lx 440H | 1,440Wx3,220Lx 470H | 1,717Wx3,720Lx 550H | |
Weight of the stirrer unit (ton) |
4.2 | 5.5 | 7.5 | 12 | |
Blower capacity for cooling coil (KW) |
7.5 | 11 | 18.5 | ||
Suppied electric source by customer |
1) Input (KVA) |
50 | 70 | 100 | 150 |
2) Voltage (V) |
220/200 | 220/200V, 440/400V | 440/400 | ||
3) Frequency (HZ) |
50/60 | ||||
4) Phase (φ) |
3 | ||||
Inverter Panel Dimensions (mm) |
W2000xD700xH2100 | W3000xD900x H2100 | |||
Control Box Dimensions (mm) |
W320xD200xH490 |