Vibrating Dryer-Cooler System
Soft and gentle to materials, continuous processing in one machine, hygienic and easy to clean
As a leading manufacturer of vibrating equipment, Sinfonia Technology manufactures a wide variety of vibrating equipment that is essential for powder/granular processing. We have already demonstrated our superior performance in a wide variety of powder/granular treatment processes in the food, chemical, pharmaceutical, ceramic, and metal industries, and have demonstrated our outstanding ability to improve quality and productivity.
This unique vibratory drying/cooling system is the result of our experience and know-how, and its unique operating principle of vibration and airflow effect enables ideal drying/cooling of any powder/pellets. We can provide the most suitable system according to the individual needs of each user, such as the type of material to be applied, its physical properties, the amount to be processed, the purpose of the process, or the installation conditions.
About Vibrating Dryer
Vibrating Equipment Ensures Uniform Fluidization
If the fluidization of materials flow is inadequate, uneven drying and cooling occur. Even materials with different particle size and different specific gravity can be conveyed with our special vibrating technology. Hot and cool air currents are also used to fluidize materials involved; each and every particle is uniformly dried and cooled.
Vibration System Allows Precise Control of Residence Time
If uniform drying and cooling is not enough, precise control of the temperature and moisture content is needed to finish materials to the required specifications. For this purpose, it is essential to control the residence time during which materials are subjected to hot and cool air currents. In this vibrating system it is possible to change the vibration conditions (amplitude and frequency) and so effect total flexible regulation of residence time (conveyance time) of materials. Thus, it is possible to achieve quality control to meet all conditions.
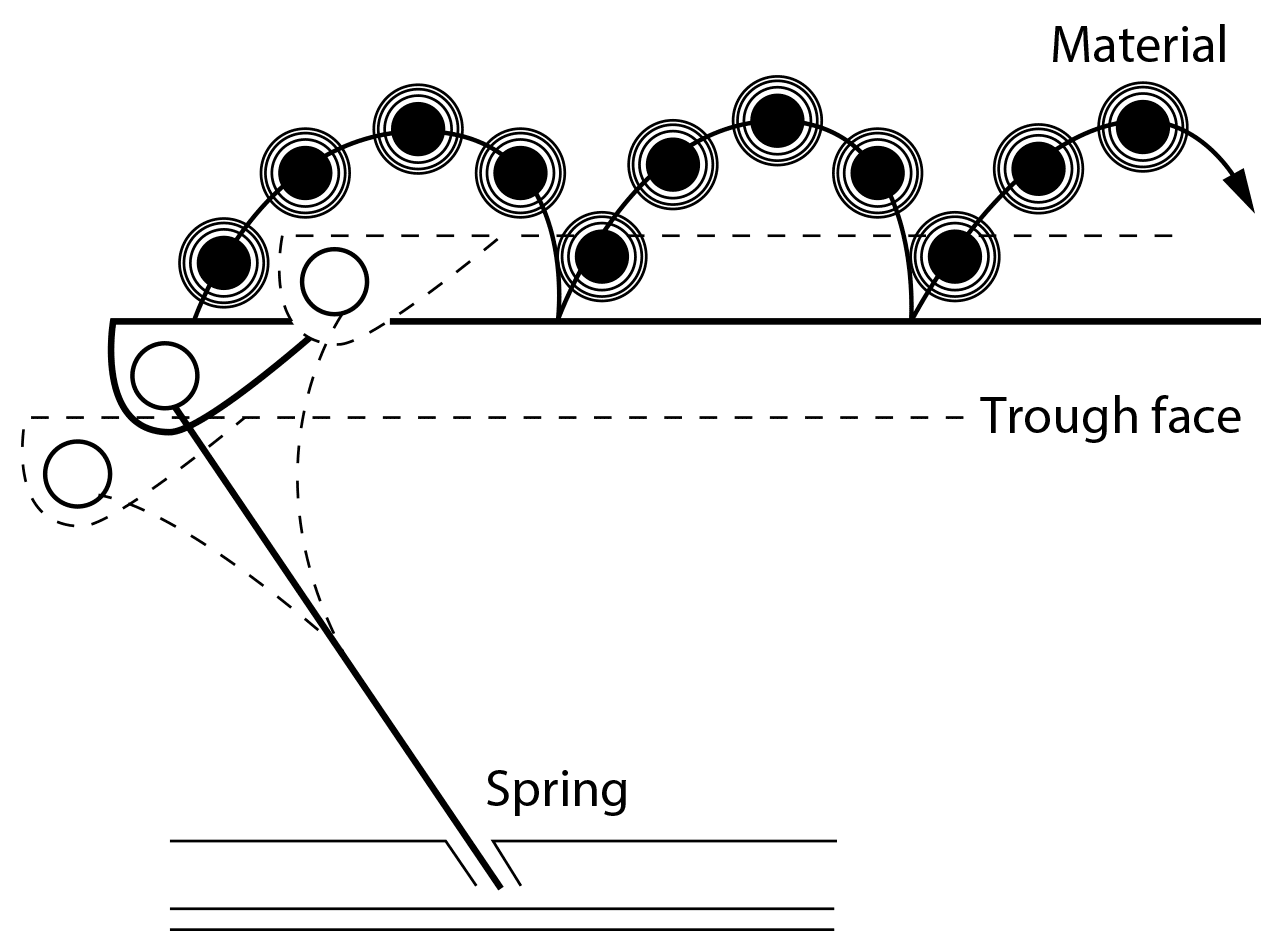
Principle of transport and fluidization by vibration
BM Type
Resonant Vibration Type
RV Type
Forced Vibration Type
Features
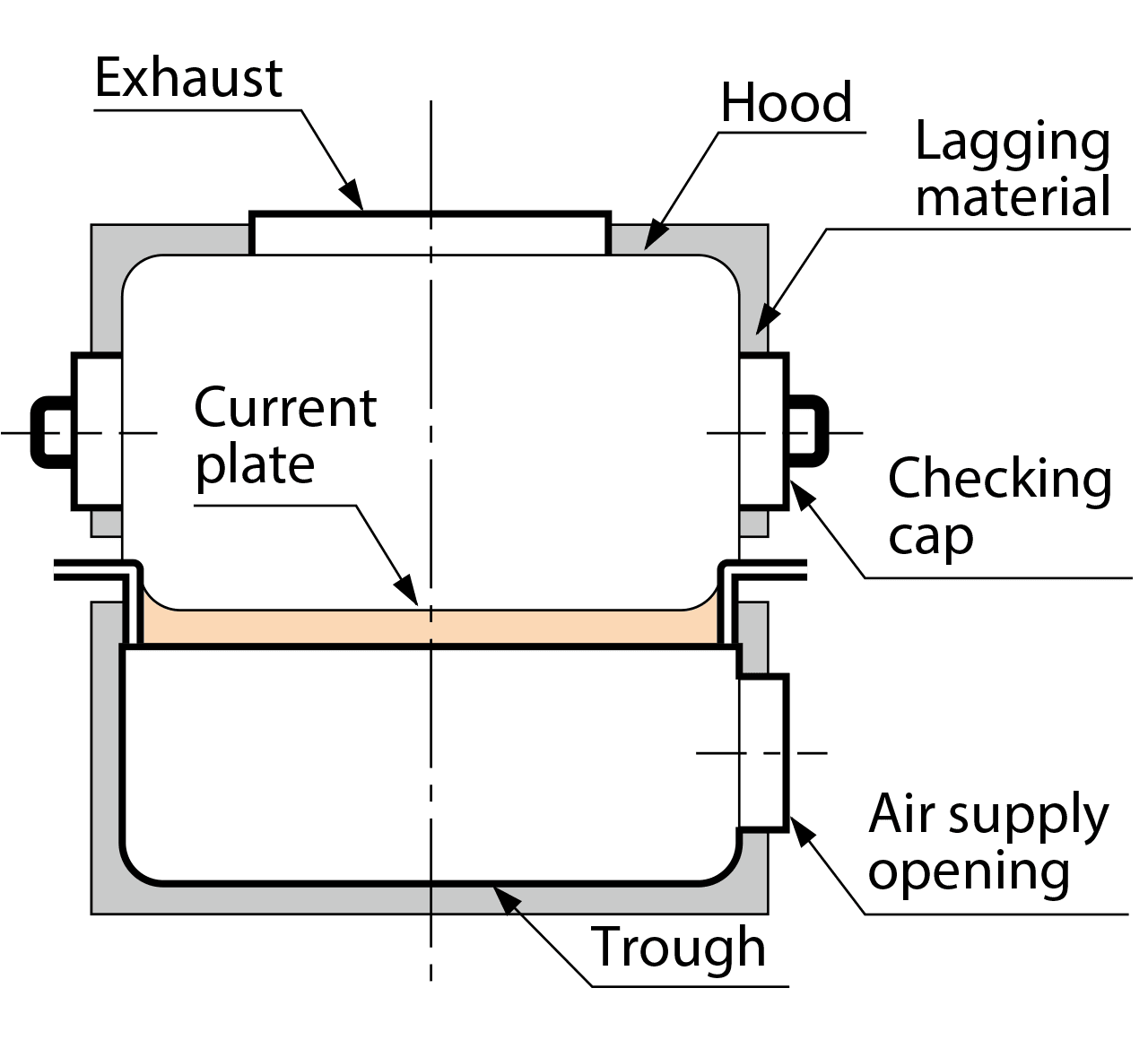
- Uneven drying and cooling are eliminated
Even materials of different grading and specific gravity can be fluidized uniformly by vibration and air currents. Drying and cooling are always carried out uniformly as the conveying speed is fixed and this results in constant residence time. - Flexible temperature and moisture control
Since the layer depth and residence time can be controlled exactly as required by varying the vibrating condition by means of electric control such as an inverter, the temperature and moisture content of materials can readily be adjusted as needed to match ambient temperature and humidity conditions. All this gives greatly improved product quality. - Materials are not damaged
As the hot air and cool air act as a cushion, shocks to the materials are reduced, and damage and loss by exhaust of materials as well as dust generation are prevented. Flakes and pellets rare not damaged or powdered. - Simultaneous drying and cooling
Since moisture content adjustment by hot air and temperature control by cool air are performed consecutively in one system, an efficient process line can be achieved. This is very suitable for drying and cooling where strict and precise quality control is required. - Energy saving and high efficiency
The power required for blowing air is greatly reduced as vibrating movement fluidizes and conveys materials effectively. Thus, this vibratory system gives far greater energy saving than other types. In addition, as heat conductivity rate is high, the unit processing capability is also large. - Can be used for materials of different grading and specific gravity
Since vibration does not allow retention of materials on the trough face, all types of materials can be evenly dried and cooled. Even powders and particles with high moisture content or those with high cohesiveness can be smoothly processed with a simple adjustment of the vibration and blower speed. - Sanitary Trough for HACCP Compliance
This HACCP-compliant device maintains a high level of hygiene with its unique trough structure. As shown in the figure below, the trough has an integral structure with rounded corners, making it extremely easy to clean. Bacteria and dirt that would easily remain in the corners of a conventional welded type trough can be washed away cleanly and a high level of hygiene can be maintained at all times.
This system consists of a vibrating conveyor as the base, a heat source (and cooling source), blower and exhaust emission (dust) control device. This system used vibrating movement to convey and fluidize the materials uniformly and the air currents from below the trough pass evenly through particles, thereby effecting consistent, highly efficient drying and cooling.
This system is ideal for use in processes where even drying and cooling, control of temperature and moisture content are vital process factors, or where energy saving and improvement of cost performance are required.
Use our equipment to improve the quality and overall productivity in your plant.
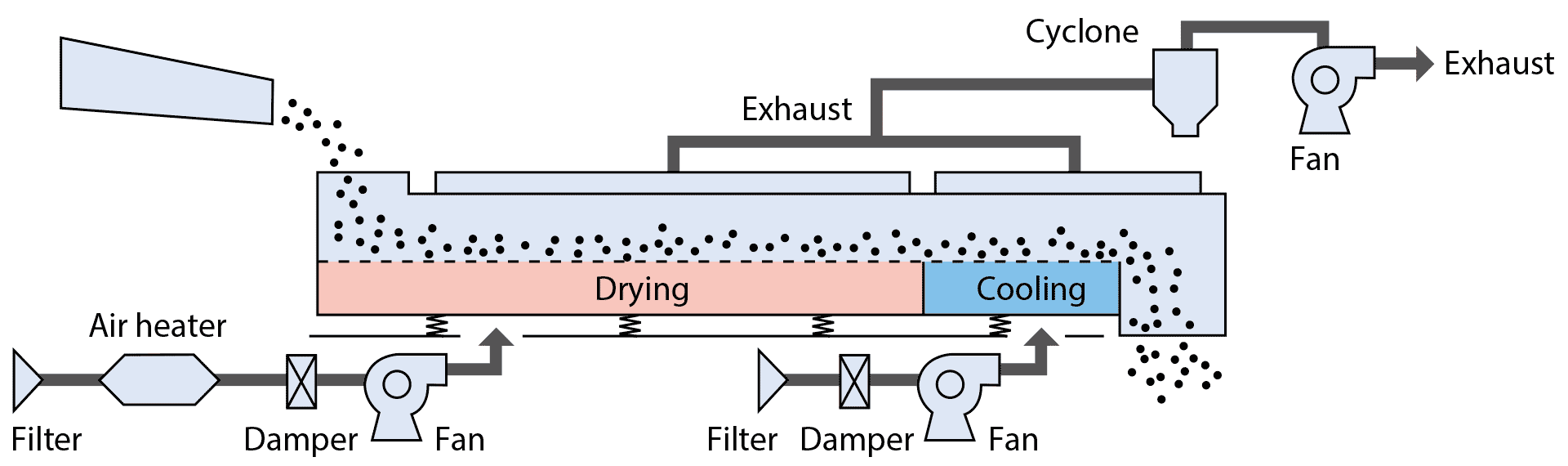
Applicable for wide variety of materials
As examples, chemical seasonings, granulated sugar, pomace sugar, grains, coffee, powdered milk, bread crumbs, chemical fertilizers, resin pellets, various chemicals, activated charcoal, foundry sand, quicklime, etc.
In addition, it can be used for drying and cooling a wide range of powdered and granulated raw materials in the food, chemical, ceramic, and metal industries.
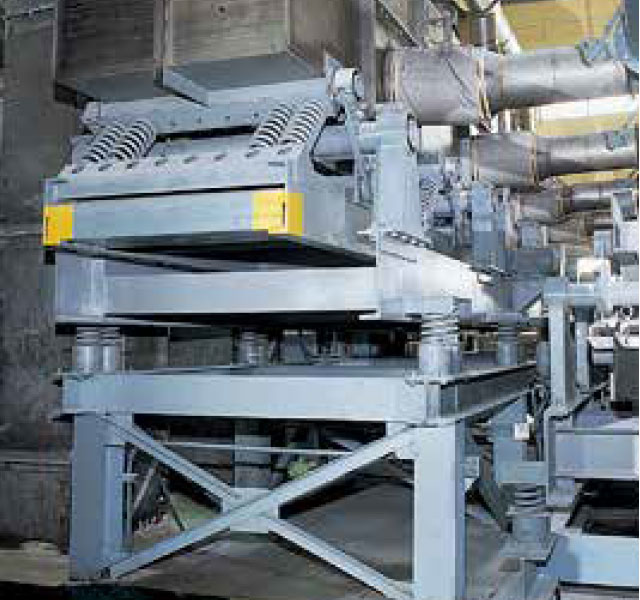
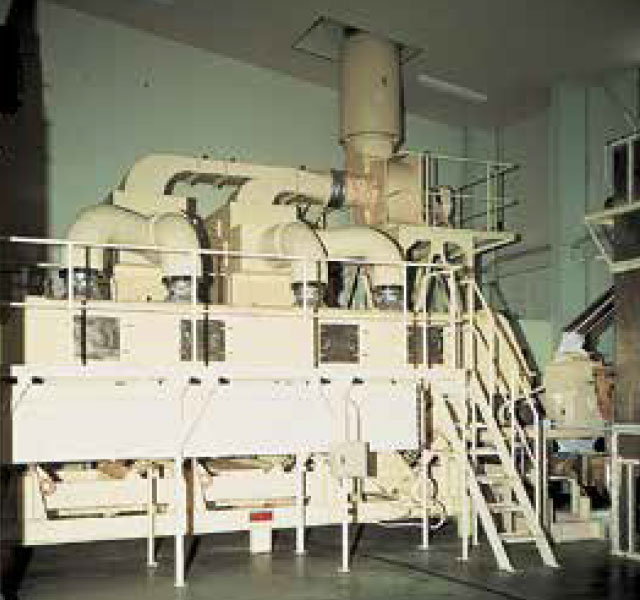
Change in residence time by adjusting the frequency
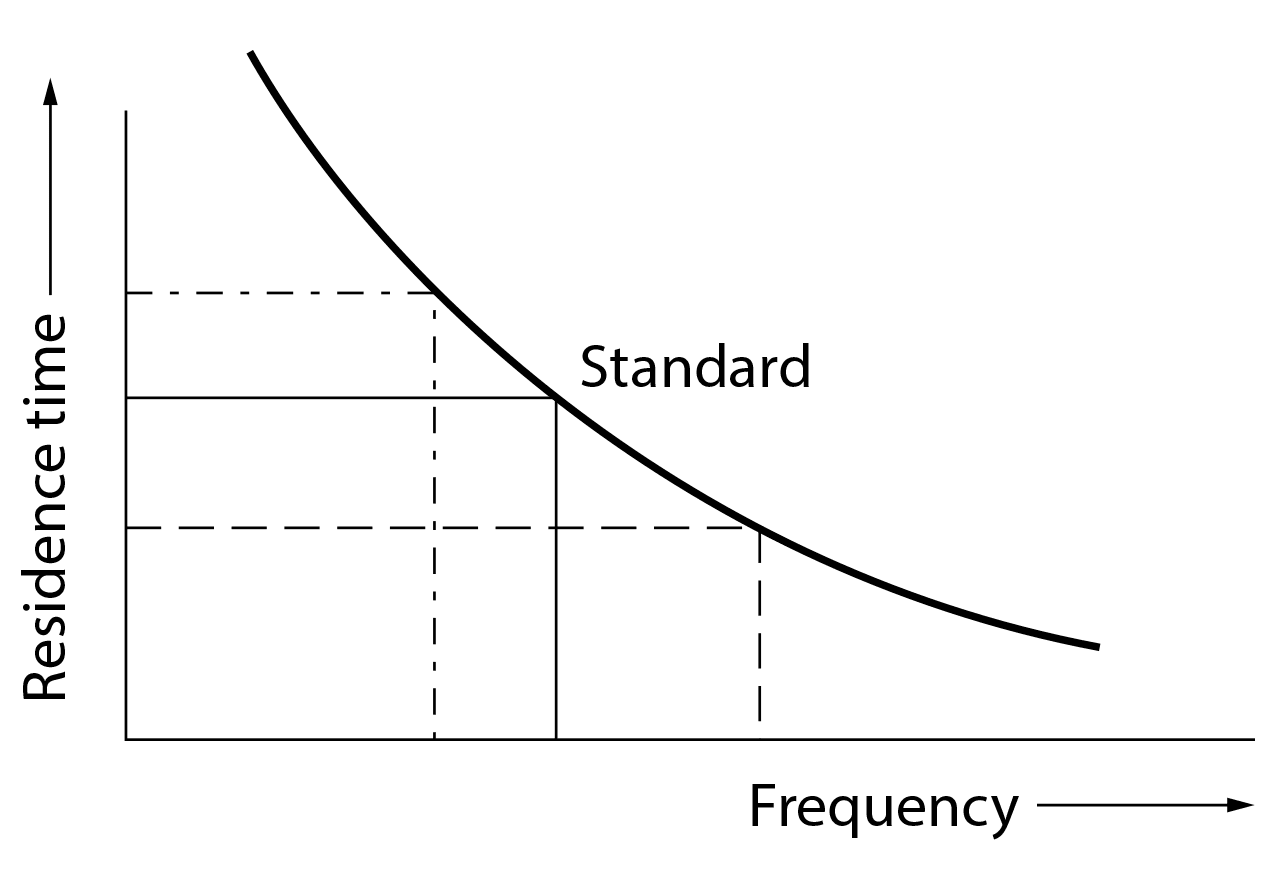
State of fluidization by air flow
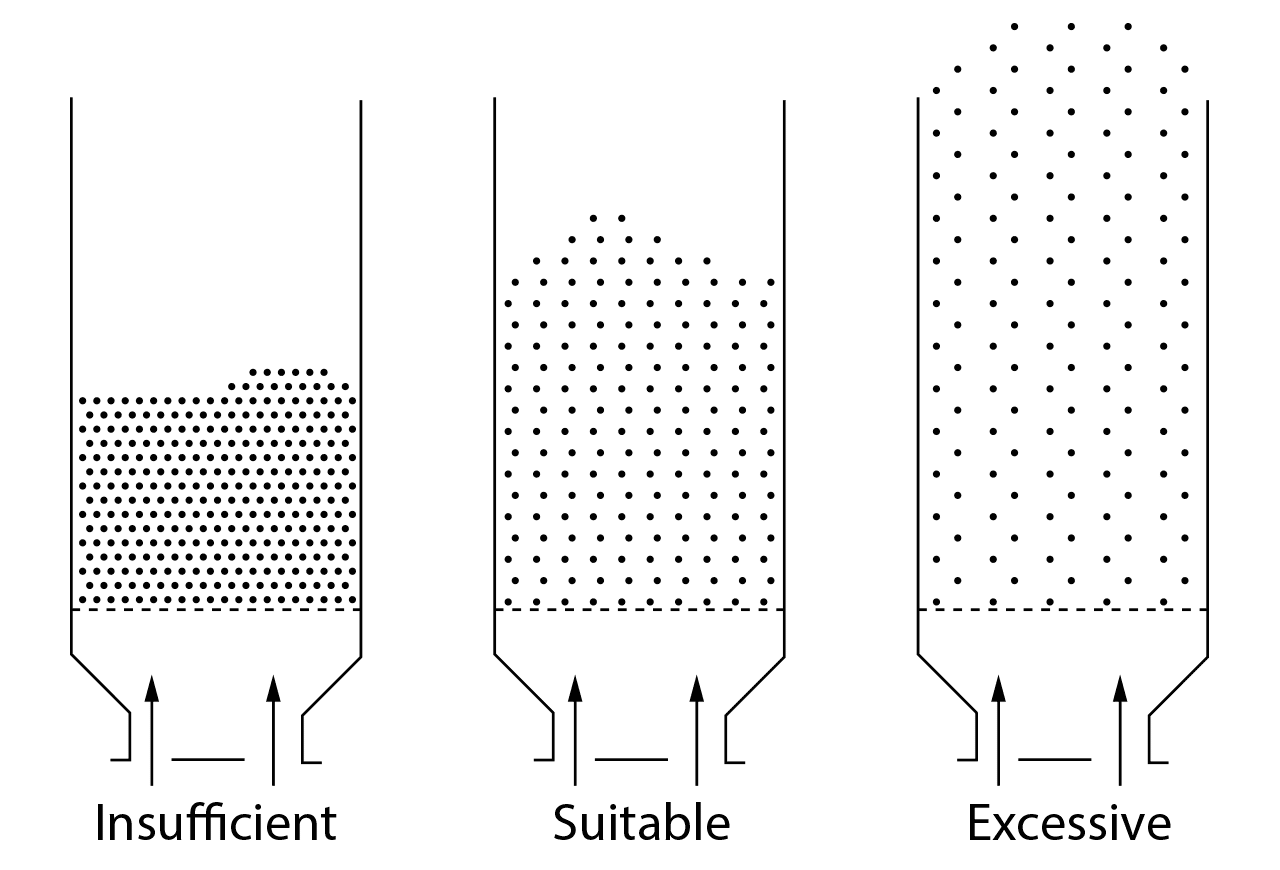
Comparison of wind speed selection range
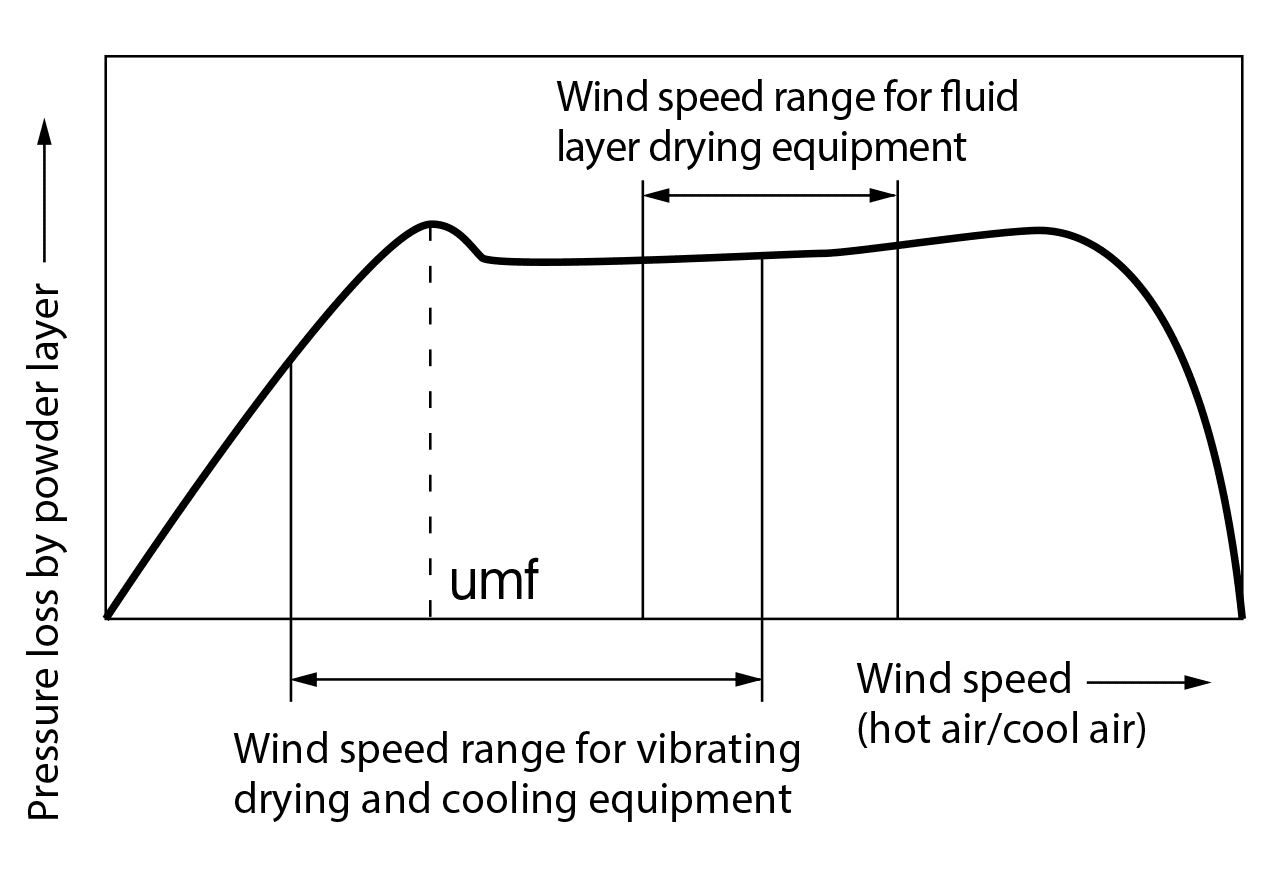
Drying Method Comparison
Item | Dryer | ||||
---|---|---|---|---|---|
Vibrating dryer | Fluid-bed dryer | Band dryer | Rotary dryer | Flash dryer | |
Material carrying mechanism | Vibration+ Fluid bed |
Fluid bed | Conveyor (Fluid bed + with rake) |
Rotary shell | Air stream |
Material coverage | Wide | Limited (Powder- particle only) |
Moderate | Limited (No cohesive and adhesive materials) |
Limited (No adhesive materials) |
Particle damage | Less | Less | Less | Some | Some |
Drying time adjustment | Easy (Residence time varies less) |
Fair (Residence time varies widely) |
Easy | Difficult | Difficult |
Heat efficiency | High | Middle | Middle | Middle or low | Middle |
Hot air volume | Controllable | High | Middle (Limited) | Low (Limited) | Low |
Carrying power | Large | Large |
Small |
Large | Small |
Equipment cost | Low | Low | Middle | High | Middle |
Install space | Small | Middle | Large | Large | Middle |
Dust loss | Less | A lot | Less | Middle | A lot |
Detergence (Maintenance) | Very good | Good | Hard | Bad | Little hard |
System Configuration
We undertake whole processes from planning, designing, manufacturing, through constructing.
Our best vibrating dryer-cooler system for granular materials has excellent sales achievement under food industries. It has a good reputation with our clients because of its high quality, high efficiency, and high reliability even though it is easy to handle. Our company delivers vibrating dryer-cooler system in total system as to client’s needs. We provide the best dryer-cooler system with newest technology and experienced technique, and also we undertake from planning, designing, manufacturing, to constructing.
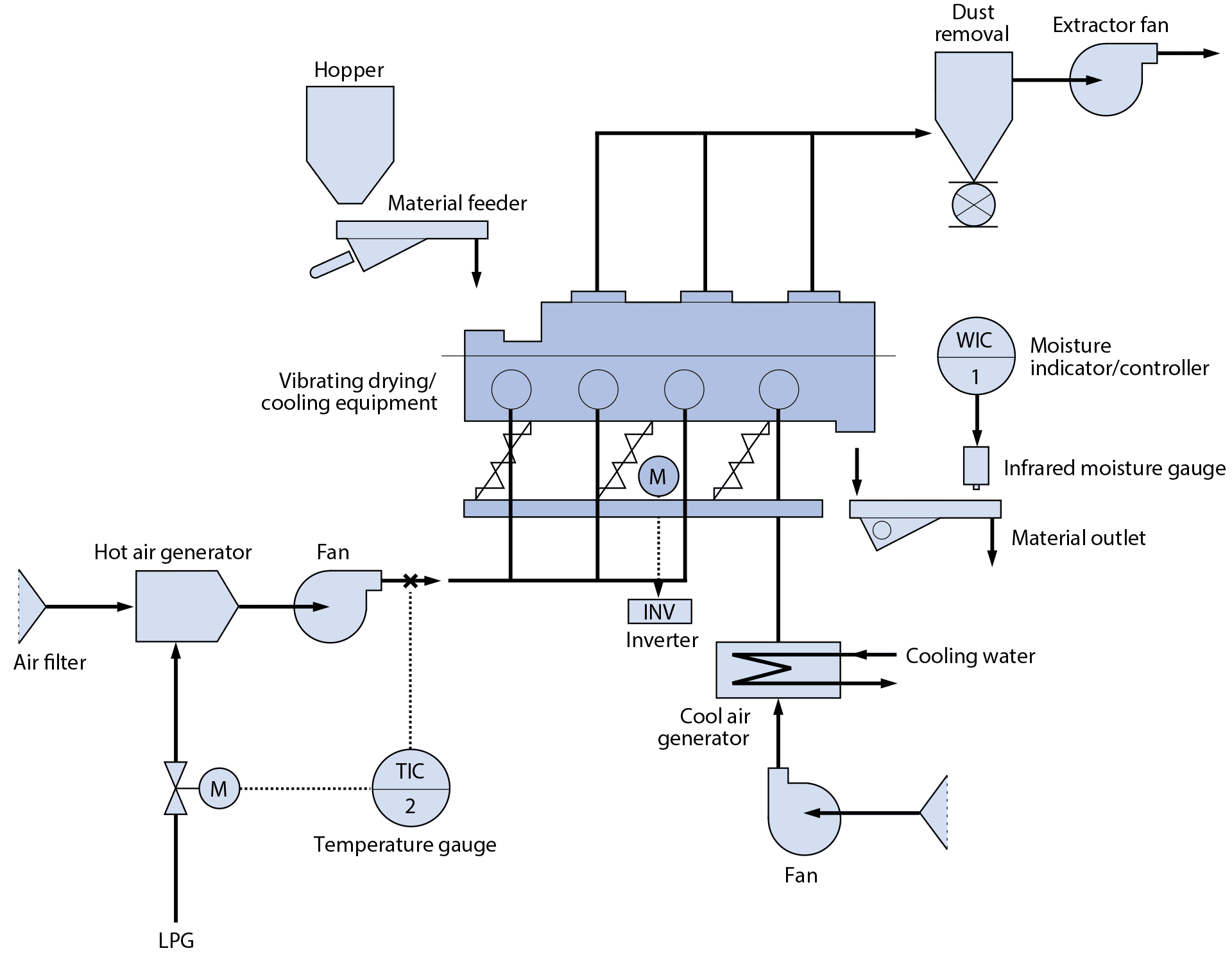
Example of application
Grain sterilizing dryer-cooler system
This is a proven example of high quality dryer-cooler system used after the steam sterilizing process of grains such as buckwheat. It enables drying and cooling without damaging the material, which is ideal for material secondary process. Instead of heating the buckwheat in powder condition as before, this system rapidly dries and cools the steam-treated buckwheat in grain. Therefore, the heat temperature will not reach the material contents. This system enables to sterilize the material equally without losing property, which is the most characteristic feature.
Processing performance: In the case of buckwheat kernel, viable bacteria count is under 10³coliform group count negative.
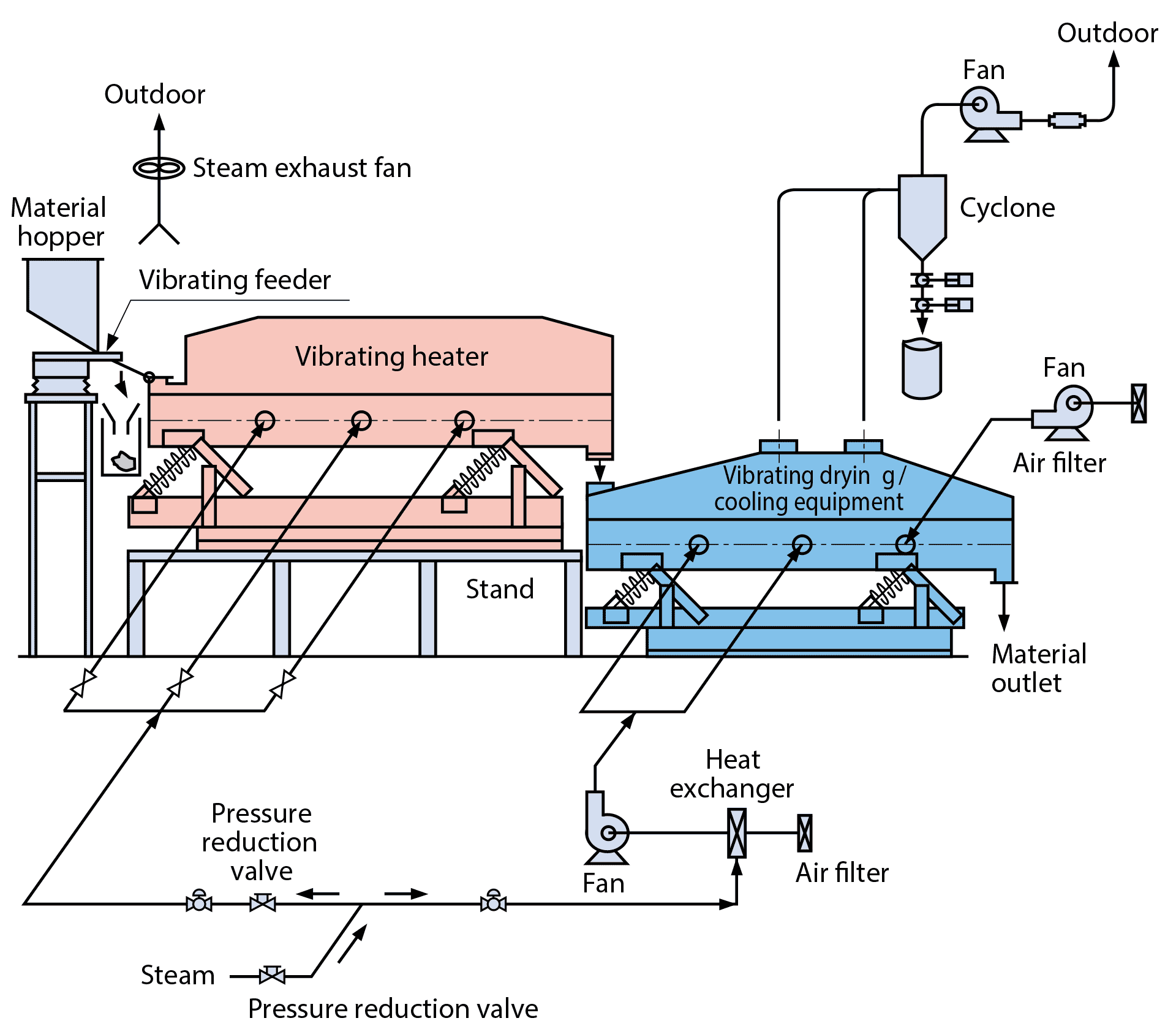
Dryer-cooler system for frozen bread crumbs
Drying and cooling process of frozen bread crumbs are required to keep high quality and sever humidity control. By the use of this vibrating system, products are fluidized evenly and smoothly, uniformly-processed without damage and become uniformly dried, while conventional stationary fluidized bed dryer-cooler system have disadvantages such as low efficiency, uneven and various drying results.
Moreover, this vibrating 2 in 1 system enables efficient use of space.
Specification |
|
---|---|
Model | DCBM-1350-6.3 motor 5.5KW6P |
Material |
Frozen bread crumbs |
Processing capacity | 1300kg/Hr |
Drying conditions |
Inlet moisture: 38% Outlet moisture: 11~30% |
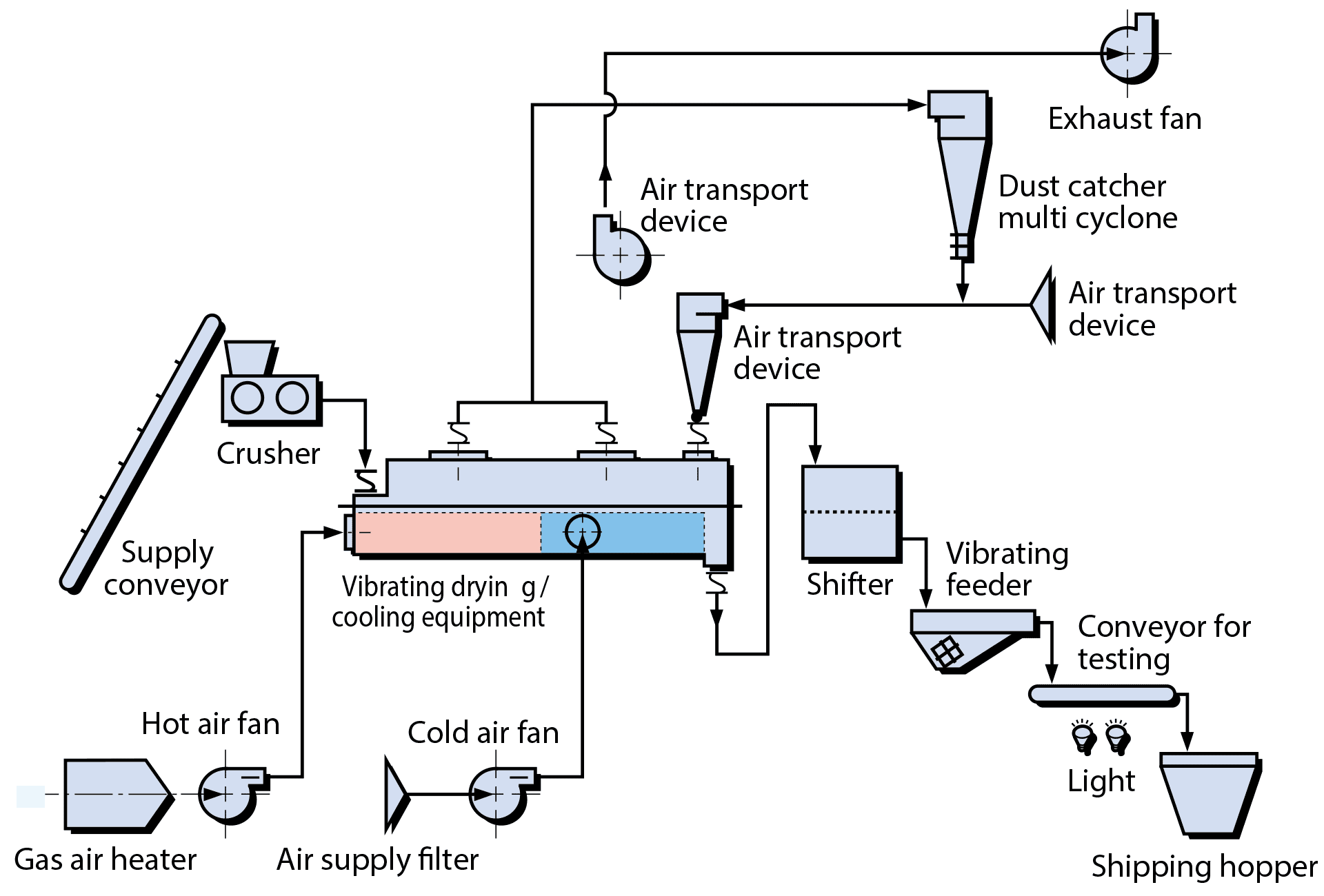
Case of Application System
Cooling system for synthetic rubber
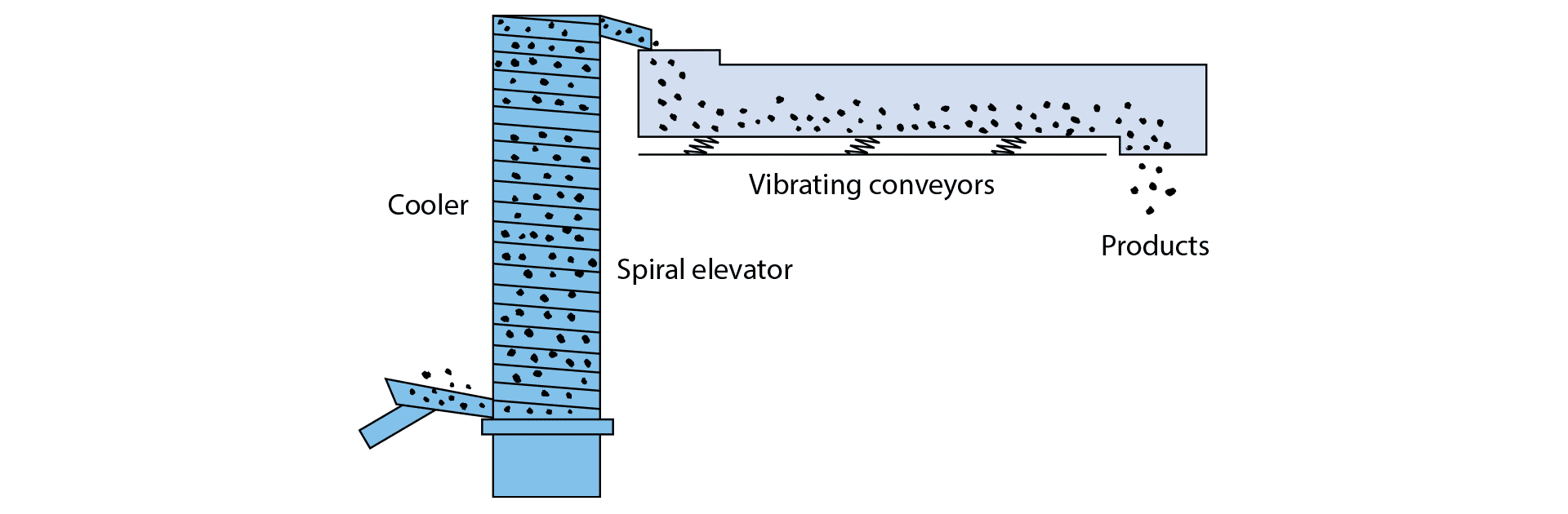
Drying and cooling system for coffee powder
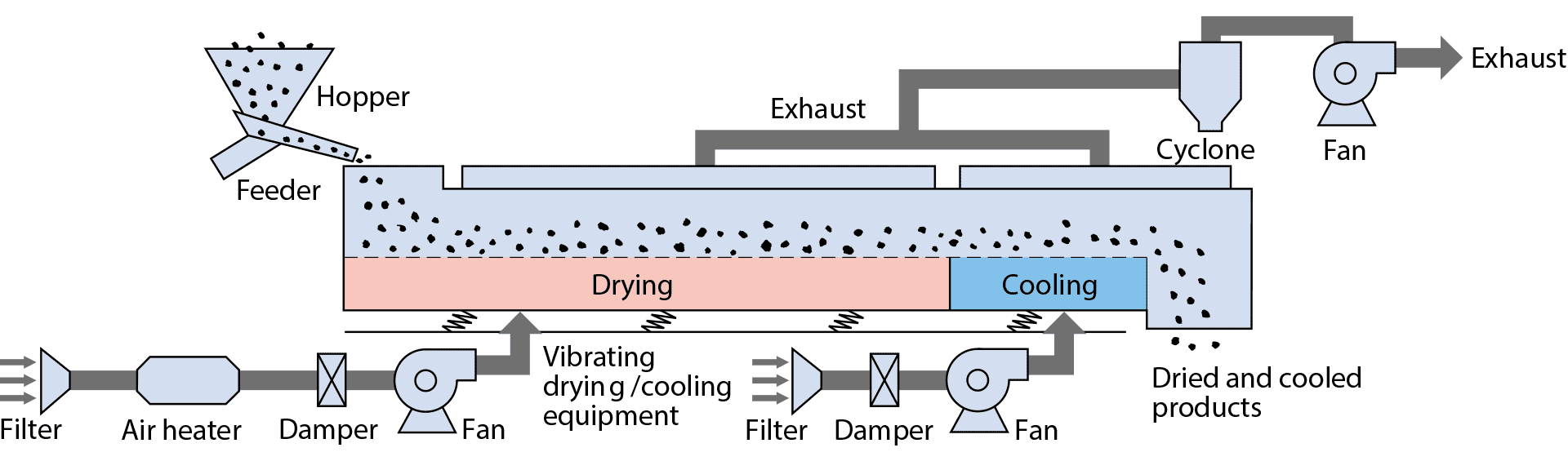
Drying and cooling system for chemical seasonings
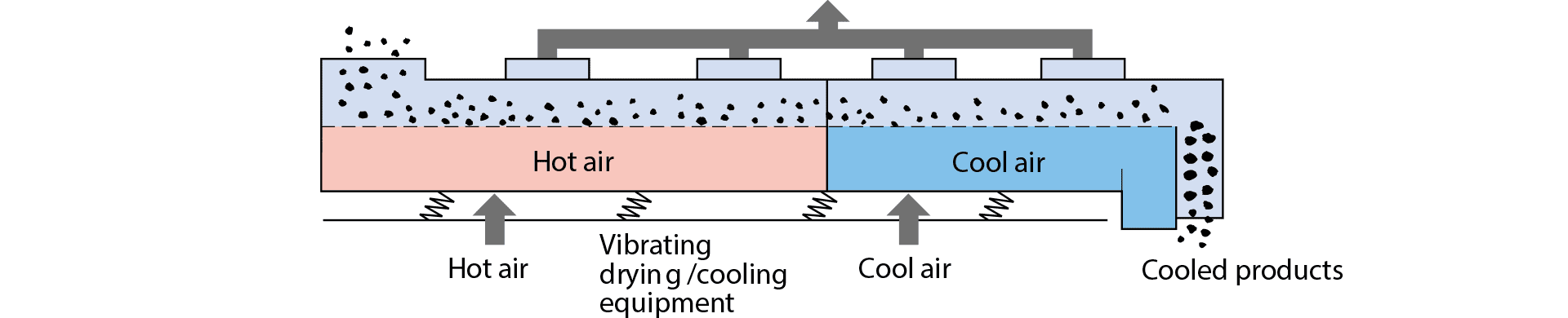
Water cooling system for quicklime

Cooling system for high-temperature brick materials
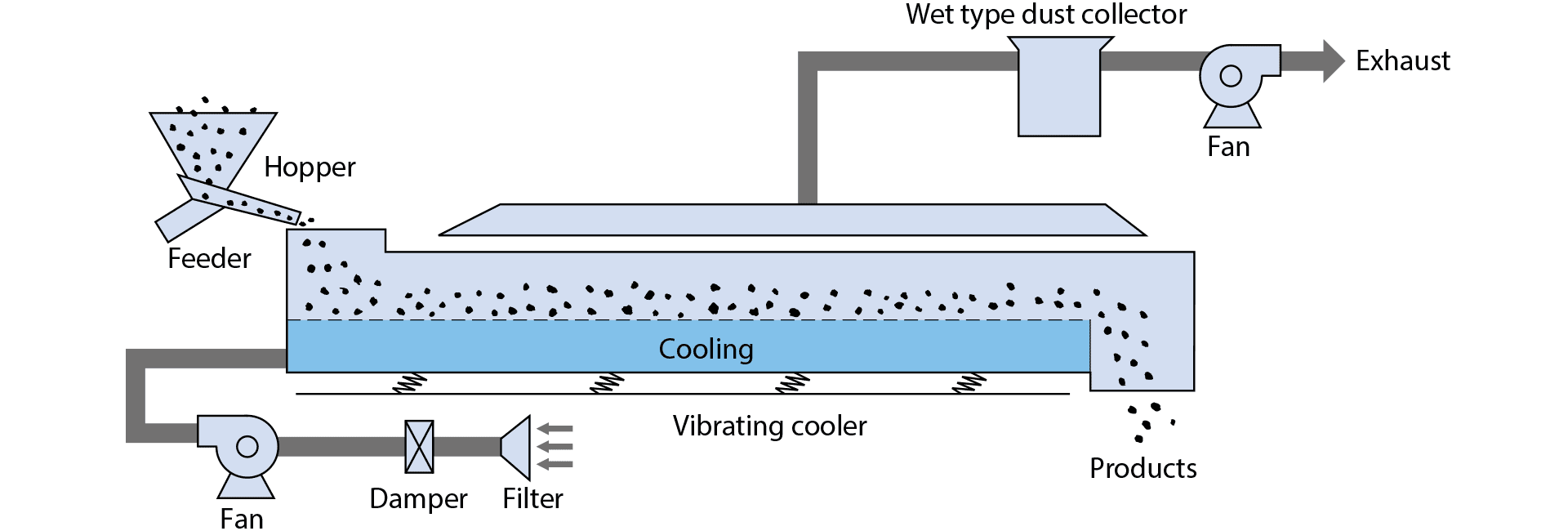
Drying system for coke
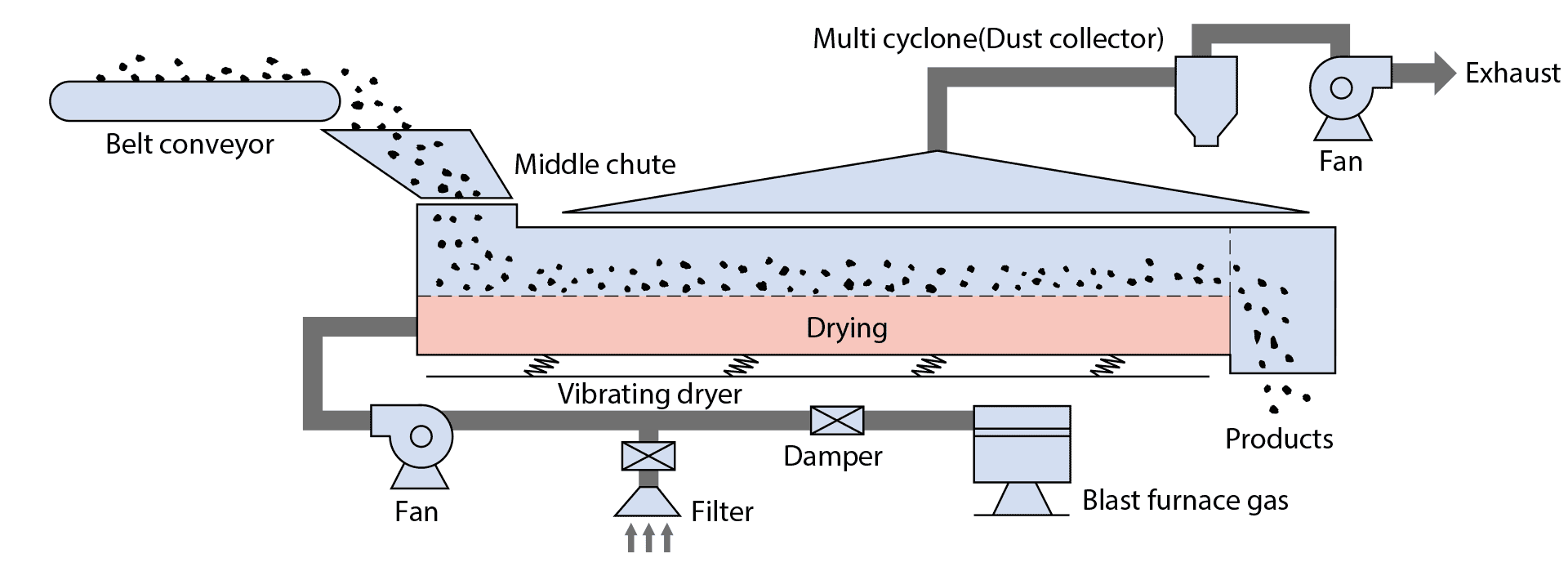
Dehydration and drying system for vinyl chloride
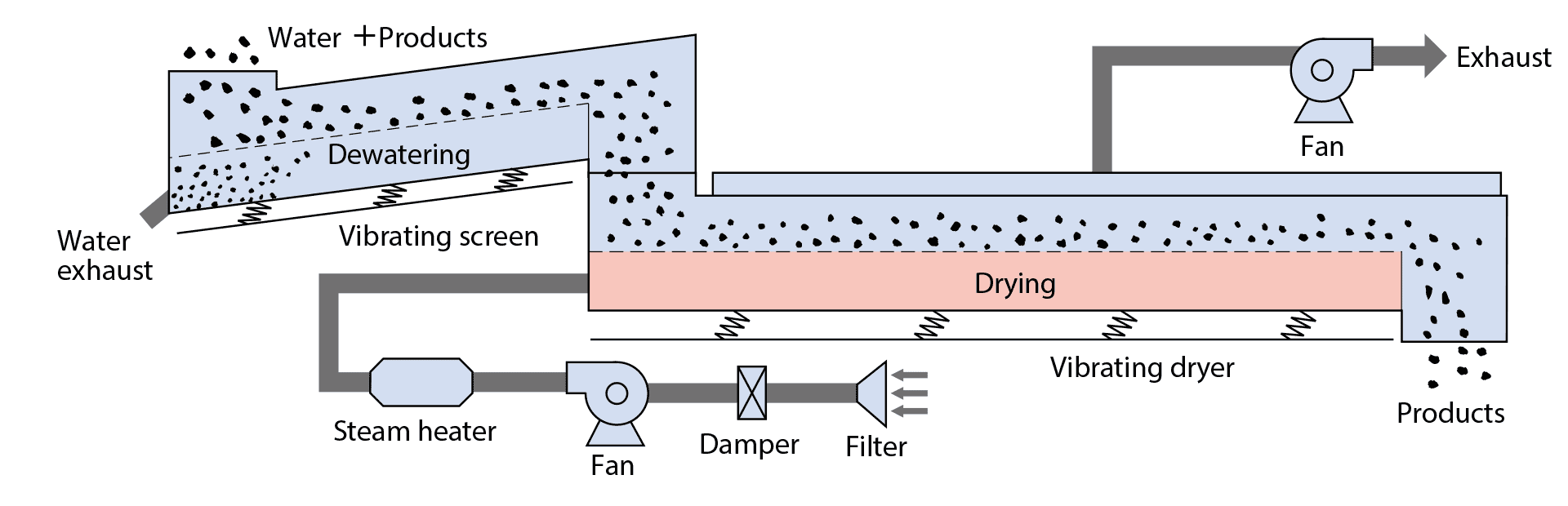
Delivery Records
DCBM
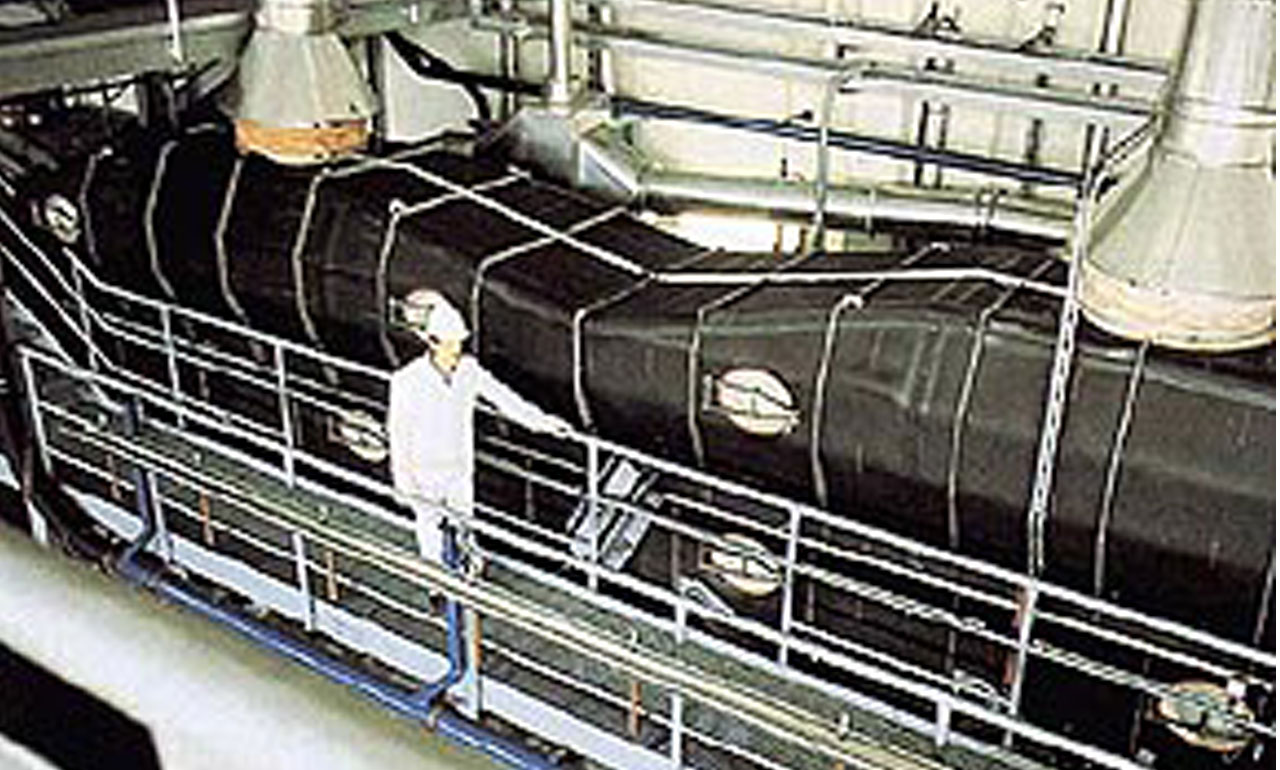
DBM
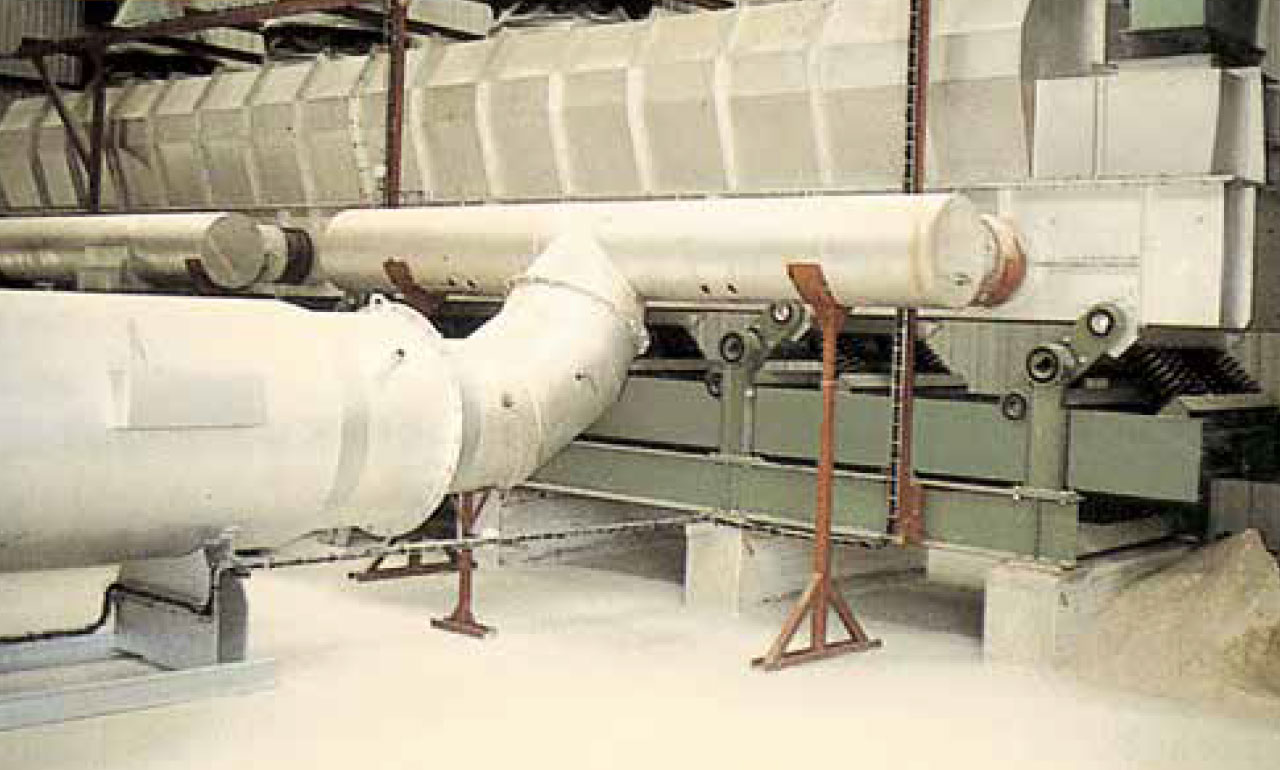
DBM Type
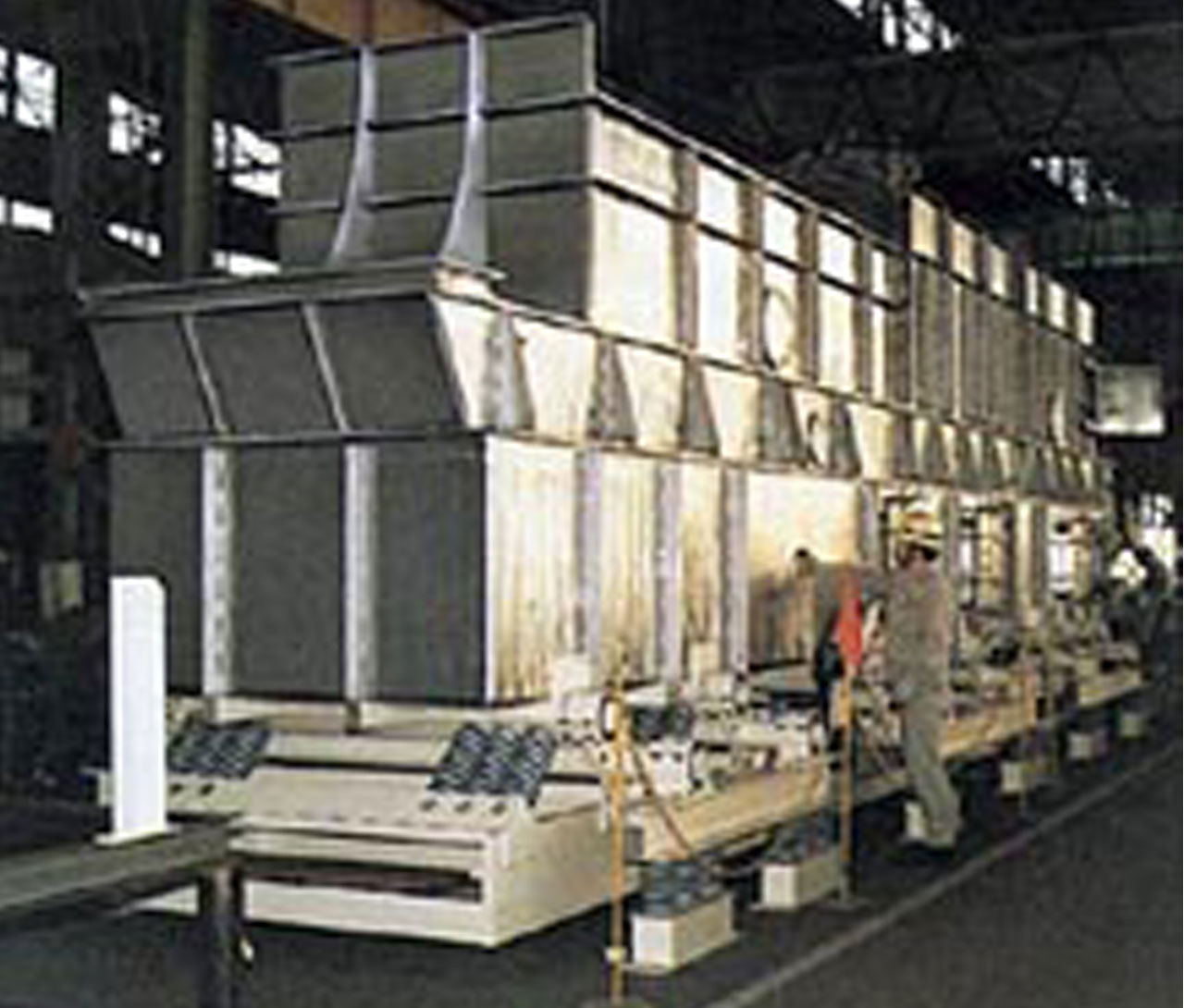
DRVF Type
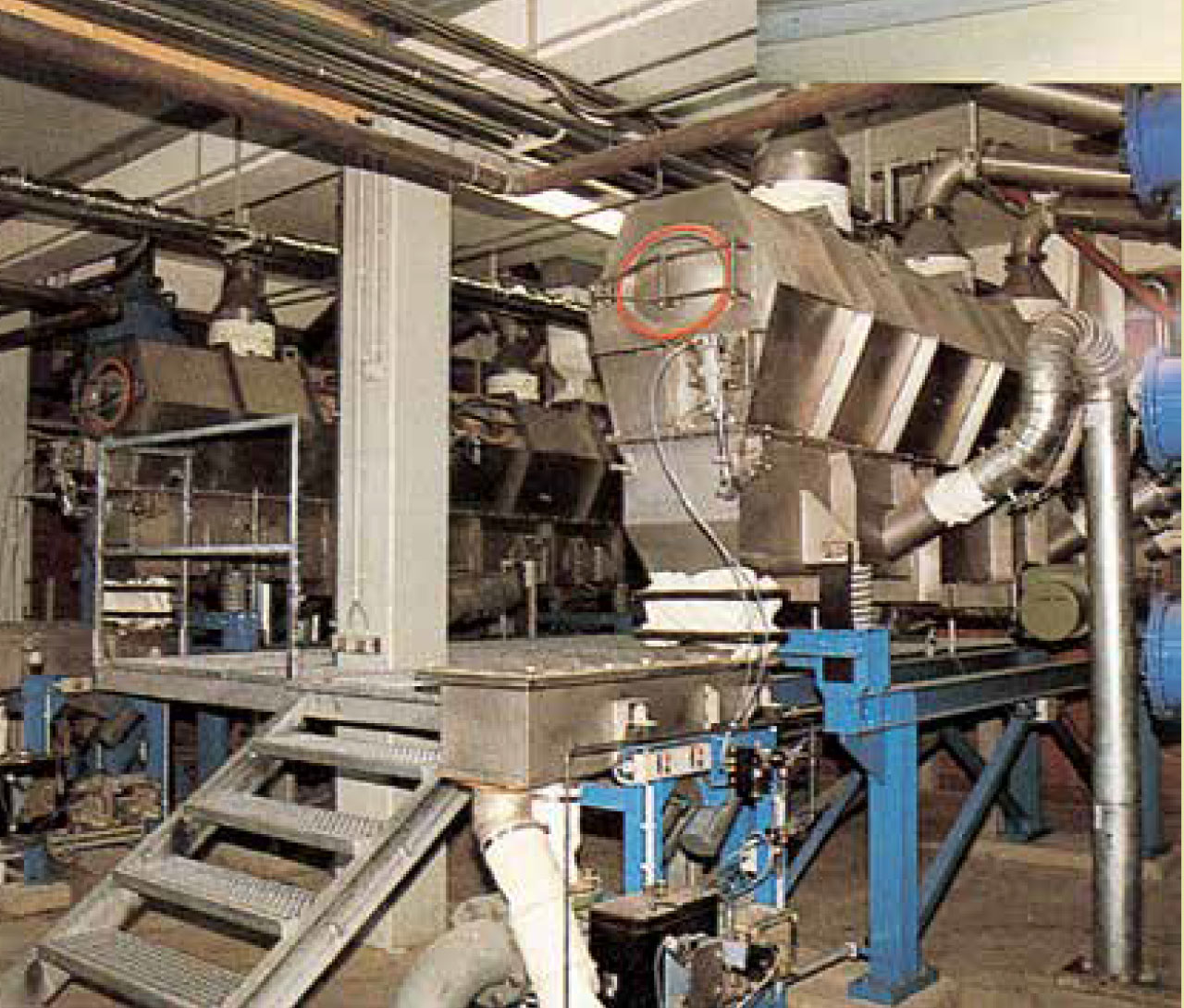
DRVES Type
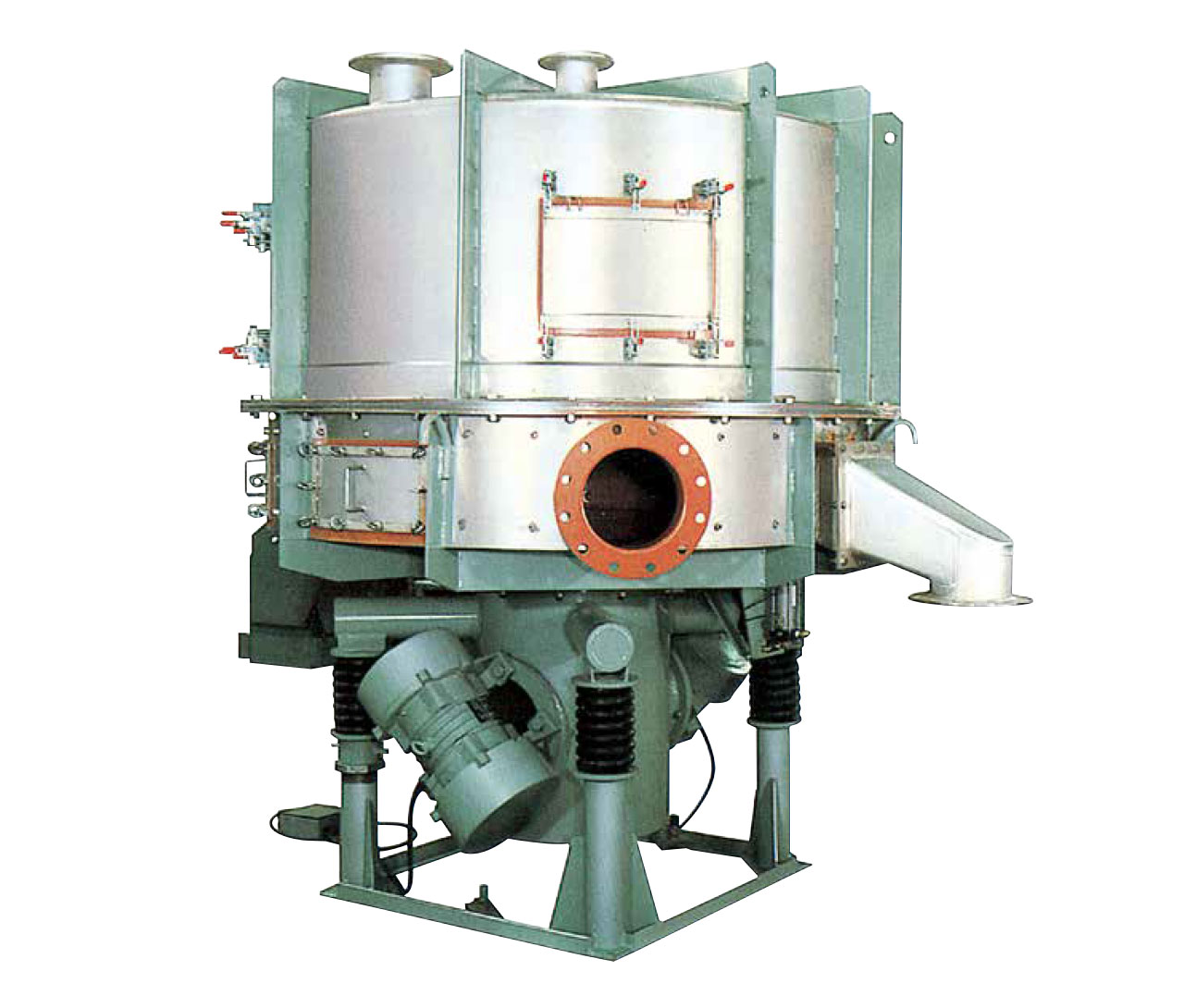
List of Major Supply Records
Model |
Handling materials |
Processing capacity (Kg/Hr) |
---|---|---|
DCBM-1350-6.8 | Bread crumbs | 1300 |
DCRVF-300-2.5 | Cornstarch | 60 |
DCBM-750-8 | MSG | 2000 |
DBM-450-5 |
Dry soup |
900 |
DCRVF-450-3 |
Instant coffee |
75 |
DCBM-1500-19 |
Granular sugar |
30000 |
DBM-750-15 |
Rice chip |
1700 |
DCBM-750-7 | Salt | 3500 |
DBM-750-15 |
Rice biscuit dough |
1700 |
CBM-1200-8.2 |
Glucose sugar |
2300 |
CMVCB-600-7.7 |
Curry powder |
2500 |
DBM-2000-6 |
Soya flake |
50000 |
DBM-1500-6 |
Corn gluten meal |
2000 |
CBM-600-4 |
Flour |
1000 |
DCBM-1800-11.8 |
Powdered milk |
1000 |
DBM-900-4 |
Colesseed |
15000 |
CRVF-450-2.4 |
Corn |
700 |
DCBM-900-11.6 |
Powdered Oyster shell |
6000 |
DCBM-1200-9 |
Soy protein |
1500 |
DCBM-900-7 |
Buck weat |
3000 |
CBM-1350-8 |
Powdered milk |
3500 |
DBM-600-6 |
Sesame |
4000 |
DCBM-900-10 |
Raw chocolate |
800 |
DCRVF-600-4.5 |
Dried sardine |
230 |
DCBM-1500-10.5 |
Pet food φ5.3×13~15φ9×9~11 |
5550 |
DBM-1200-11.0 |
Fish meal (For yellowtail) |
1200 |
CRVF-900-4.5 |
Fish meal (For yellowtail) |
1200 |
DBM-1500-17 |
Fish meal (For shrimp) |
1850 |
DCBM-1500-7.8 |
Fodder pellet φ3.5, φ4.5, φ6.0 |
15000 |
DCBM-2000-7.8 |
Foder flake Maize, milo oats, barley |
15000 |
CMVCB-450-3.5 |
Vinyl chloride pellet |
1500 |
DBM-600-4.6 |
Phenol resin |
400 |
DCBM-450-4.5 |
Phenol resin |
300 |
CRVES-780-2.05 |
Urea-melamine cast material |
150 |
CMVCB-600-4 |
Tetronic pellet |
2000 |
DBM-750-3.4 |
Hard vinyl chloride |
1200 |
Model |
Handling materials |
Processing capacity (Kg/Hr) |
---|---|---|
CMVCB-300-8 |
Nylons chip flake |
100 |
DBM-12000-9.4 |
PCV compound chip |
14500 |
CBM-750-4 |
PVC pellet |
2600 |
CRVF-600-4.5 |
Poval |
2000 |
CMVCB-1050-4 |
ABS pellet |
3600 |
DBM-450-10 |
Thermo-setting resin |
700 |
DBM-1200-5 |
Polyacrylamide |
600 |
DCBM-600-6 |
Phenol resin |
- |
DBM-1600-13 |
Rubber crumb |
5000 |
DBM-1050-5.5 | Synthetic rubber | 3200 |
DBM-1200-12 | Synthetic rubber | 4600 |
CMVCB-600-6 | Ammonium nitrate granulate | 5500 |
CMVCB-1050-5.5 | Soap powder |
4000 |
CBM-1200-12 | Chemical sod |
6000 |
DCBM-1200-7.45 | Granular calcium chloride |
4000 |
DBM-300-7.5 | Caustic silver | 300 |
DBM-900-6 | Calcium phosphate | 1500 |
DCSBM-750-5.8 |
Dinitronaphthalene |
400 |
DCBM-450-3.5 | Ammonium sulfate (natrium) |
350 |
CRVF-300-2 | Phosphate | 200 |
DRVES-1800-1.1 | Catalyzed hydrogenation of terephthalic acid | 117 (/30minutes) |
DRVES-1200-5 | Electrolysis manganese dioxide |
2500 |
CBM-1500-8 | Sulfur pellet | 2000 |
CMVCB-1200-4.9 |
Magnesium hydrate |
1800 |
CBM-7500-7.5 | Granular calcium chloride |
600 |
CRVF-600-4.6 |
Ammonium sulfate |
11000 |
DRVF-500-2.3 | Enzyme drug |
120 |
CMVCB-750-2.4 | Iron oxide |
200 |
DCBM-600-9.2 | Magnetic powder |
400 |
DBM-900-5 | Electro melting alumina (Abrasive) | 1500 |
CRVF-300-2.5 | Alumina ball | 300 (liter/H) |
CRVES-650-0.8 | Powdered ferrite |
250 |
CBM-1200-12 | Chemical fertilizer |
15000 |
CMVCB-750-7.5 | Silicate-calcium fertilizer | 11000 |
DBM-1200-7.9 |
Chemical fertilizer |
50000 |
CMVCB-750-8 | Chemical fertilizer | 9400 |
CBM-450-7.6 | Burnt lime |
3500 |
DCBM-1050-10 | Pelletized original soil for nursery soil |
6600 |
DMVCB-1200-14 | Magnesium fertilizers | 18000 |